PECVD System Control Panel and Integration
Two Plasma Enhanced Chemical Vapor Deposition chambers with a shared Airlock needed a control system to integrate the various instruments, and provide a convient method to control and store data. An Automation Direct Productivity PLC and CMore HMI was called upon to meet the customers requirements at the most economical point.
Click this heading for more info!
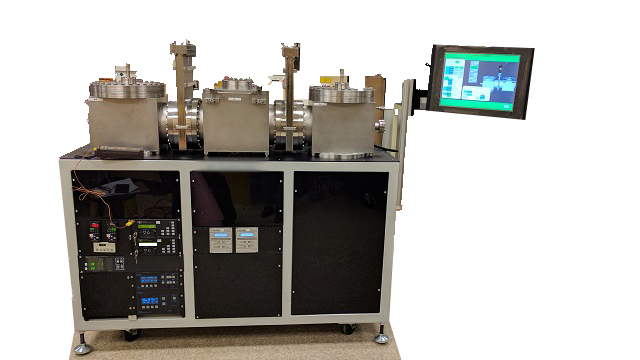
Fanuc Robotic Workcell
Arapahoe Controls provided the Engineering and Design of a Fanuc robotic workcell. The six axis robot was fed by a set of conveyors coming off of four CNC milling machines. The workcell integrated Fanuc's new Dual Check Safety (DCS) fencing and light curtains.
Safeway Bread
Arapahoe Controls provided the
control system for a set of conveyors that
route loaves of bread from a cooling unit to
three automatic slicer and bagger machines.
Click this heading for more info!
Speed Stacks
Speed Stacks required a quick integration of a controller with a fixture they designed and built in-house.
It consisted of a GE Fanuc VersaMax Nano PLC with
an expanded output module. Input was a simple pushbutton
and output was to a bank of 8 indicator lights and 6
pneumatic cylinders.
It interfaced with a Banner PresencePlus vision system.
There is a series of 20 test steps the PLC paces the vision
system thru. Each step either continues, or stops execution
and lights the appropriate indicator lamp with the test results.
The program number is sent from the PLC to the vision system via.
a pulse train specific to each test file in the camera. The vision
system acquires and analyzes each image and sends back a pass/fail.
The timer is advanced thru it's functions by small cylinders pressing
the buttons on it's keypad. Each function is verified by the vision
system looking at the LCD display and LED indicators on the product.
SMT Microchip
Tester
This is a two sided workcell, both are nearly identical. The product
is a matrix of components of various numbers of rows & columns. A pair of MicroLogix PLC's
are interfaced with PanelView OIT's and Yamaha RX222 dual axis motion controllers.
The principle
of operation is for the PLC to act as the master controller, directing
a Yamaha dual axis robotic slide, and a digital testing unit to
test the product row by row. The PLC will track faulty parts, and when
the testing is complete, direct the robot to the locations with faulted
parts and removing them by a vacuum pickup.
There are also several diagnostic capabilities that have been programmed
into the PLC. The vacuum system is verified by removing product in a
pre-defined "X" pattern. A re-test option is available to verify that
faulty parts have been removed.
Several runtime alarms have been programmed in to alert the operators
of batch problems, identified by both row and column. Variables are accessed
in the OIT to specify the tolerance of failures in each row or column,
to identify a faulty batch.
Cognex
InSight
Arapahoe Controls successfully integrated a
Cognex InSight 5400 vision sensor with an
Allen Bradley ControlLogix PLC.
Vision Tools were selected to
differentiate the proper part out of an
array of 60. The solution ended up utilizing
the CLX messaging instruction to send the part number
data to the InSight. The original plan was to use OPC, but,
the Cognex OPC compatability was only to other Cognex hardware.
Hopefully, they'll open this up soon. The customer completed
their motion end of things, and had a successful runoff.
Turret Loader and
Unloader
We provided the electrical engineering and
PLC programming for an ergonomic
improvement project to unload unwieldly
rolls of material from a beam.
The hardware was an Automation Direct DL06
PLC and SureServo drives. There were three
axis' of motion and 80+ digital
I/O.
Automated Assembly
Dial Machine
A complex series of tasks was
requested of us in providing the electrical
design and programming for a 6 station dial
table indexing machine. Three individual
components are loaded in bulk to the
workcell, and the controls process them
into a finished, inspected product.
An Automation Direct DL205 PLC with a
fully loaded local and remote rack was used
for control. Two Animatics servo motors
were also implemented along with a Camco
indexer. Display is by a 10 inch color
C-more touchscreen.
Medium Scale
Conveyor Control System
The Leanin' Tree greeting card company
in Boulder Colorado selected Arapahoe Controls to design, build, and program
the control system for their plant
expansion.
Hardware used was an Automation Direct
DL06 PLC to control the contactors for 28
conveyors.
There are several merge points for boxed
products, and lift gates all requiring
control system intervention to prevent
collisions.
Click this heading for more info!
Plus many
more... |